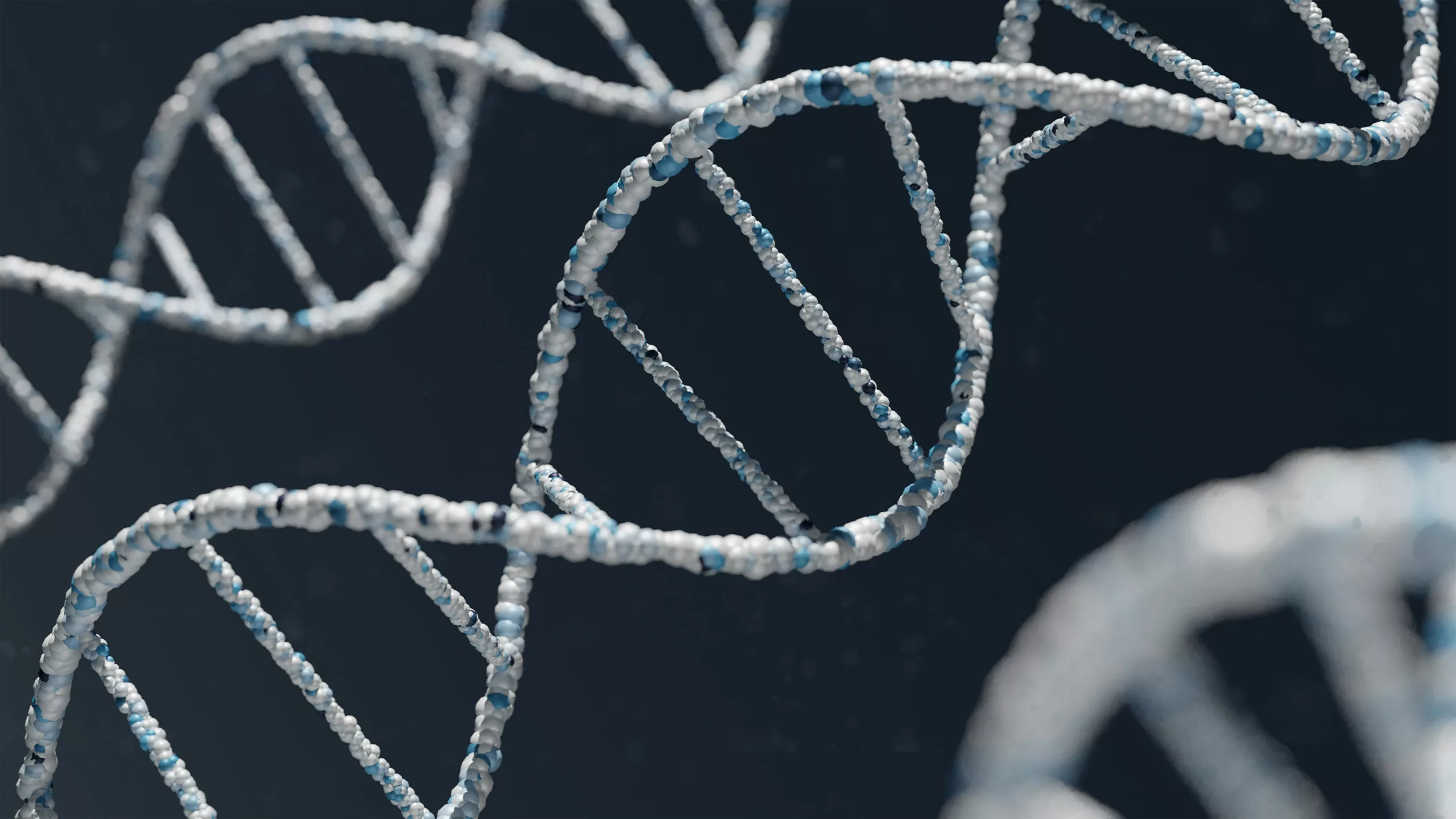
Biofoundries: opportunities to expand drug development
Research must move at a faster pace. Despite the advances made in the biotech industry, millions of people still pass away from disease today.
But it’s not for lack of trying.
In fact, we have more drug candidates going through clinical trials than ever. Even so, 90% of those drugs fail clinical trial tests. Furthermore, stories abound of drugs that worked well in clinical trials but fail to improve disease outcomes in the real world.
Building robust target discovery and validation platforms can reduce the challenges in the existing discord between clinical trial data and real-world results. It provides a way to validate drug targets and confirm a drug candidate’s activity before the clinical trial begins. Assaying drug behaviour and activity, in turn, would change the landscape for drug development.
To tap into this major development, The London Biotechnology Show came alive with a panel dedicated to precision medicine and synthetic biology. Ginkgo Bioworks took center stage during this panel, standing tall at the intersection of these two sectors.
Today, we are delighted to hear from Sidhyansh Saxena, Head of Business Development Europe at Ginkgo Bioworks. Having overseen various high-impact projects at Novartis, he is well-suited to speak into the synthetic biology industry and the ways it facilitates diverse projects across the biotech ecosystem. Through this interview, you can see how Ginkgo becoming a biofoundry accelerates precision medicine research and makes therapeutics that much more accessible.
So, we hope you enjoy this interview!Â
The Interview
PN: Let’s start with Ginkgo’s storied history. How was Ginkgo Bioworks formed?
SS: Ginkgo Bioworks was founded in 2008 by a group of scientists from the Massachusetts Institute of Technology (MIT). Their mission, which lives on today, focuses on making biology easier to engineer. We have become a biofoundry that possesses the leading horizontal platform for cell programming. We provide flexible, end-to-end services that solve challenges for organizations across diverse markets. Whether you’re in food or agriculture, pharmaceuticals, or specialty chemicals, we make producing organisms and biomolecules more efficient and cost-effective.
PN: You mentioned that Ginkgo Bioworks is a biofoundry. What is that, and how does Ginkgo being one advance the biotech industry?
SS: A biofoundry is a platform for designing and building organisms using genetic engineering tools and automation. Biofoundries enable researchers to accelerate research and development processes, reduce costs, and quickly bring innovative products to market. Such platforms are essential given the increasing complexity of redesigning and fabricating biological systems in synthetic biology.
Many biofoundries comprise several facilities within a unified complex. Each facility would possess robotic liquid-handling equipment, high-throughput analytical equipment, and intricate data management systems for running the biofoundry’s equipment. With synthetic biology taking greater prominence in biotech, we are positioning ourselves to drive the industry forward. We’re constantly improving our automation and optimization processes. We’re also scaling up our efforts to meet economies of scale. And we’re establishing more partnerships. Combined, Ginkgo Bioworks enables its partners to accelerate research and development processes, reduce costs, and bring innovative products to market faster.
PN: As your operations grew, so did your partnerships. What problems have you observed with your partners that you’ve been able to address?
SS: Our partners work in many industries that span the entire biotech industry. Despite that, they all need one thing: the ability to combine scale with flexibility. That means being able to work at high-throughput levels and customize workflows to fit a project’s specific needs. Unfortunately, most traditional automated labs are built with solutions that come with a painful trade-off between flexibility and scale. If you want flexibility, you do your lab work by hand; if you wish to scale up, you do it with an integrated work cell. Walk-up instrumentation lies in between.
PN: I can attest to many researchers not wishing to compromise with their solutions. They want as much as possible at the lowest possible cost.
SS: It’s precisely for that reason we at Ginkgo challenged ourselves to leave this trade-off behind and achieve scale and flexibility at once. And we call our solution Reconfigurable Automation Carts (RACs).
PN: That sounds exciting! Tell us more about RACs and how they help you achieve scale and flexibility.
SS: A RAC typically contains a single robotic arm that serves one instrument. Every component it needs to function can be found within its own enclosure. These include a programmable logic controller (PLC), an industrial computer, power, air, safety circuits, and more. We also include a magnetic conveyor track that moves sample plates between RACs.
PN: This sounds like mass production at its best. You make all the component RACs individually and then combine them at the final assembly.
SS: Exactly. We can put many RACs together to create a larger, modular RAC system, much like a train set. You can make many train types depending on how you arrange the passenger cars or which locomotive you start with. With RACs, you can build each RAC and reconfigure the system to meet specific needs. You can make a modular system as small as 5 to 15 RACs or prepare one as large as 185 RACs. The latter was done for high-throughput phenotyping work. That said, we usually prepare 20-25 RACs on average.
PN: That’s a lot of systems in one! What kinds of business value have you seen from this approach?
SS: RACs have been delivering business value like we’ve never seen before. To give you just a small sample of our impact, we have seen an 80-90% reduction in labor requirements when moving from traditional automation to RACs. We also decreased cycle times by 60% by being able to automate team hand-offs. We even provide a small number of support engineers in different time zones across the US. That has been possible thanks to our Automation Control Software, a modern and fully cloud-based solution that provides real-time monitoring of various RACs.
PN: I’ve heard people concerned about the high cost of preparing a biofoundry to produce biomolecules and bacteria for biotech companies. How do you anticipate Ginkgo addressing these concerns, and when do you anticipate your solutions improving profitability long-term?
SS: Our founders have experienced the challenges and costs of programming cells firsthand. From our humble beginnings, Ginkgo spent years to achieve a cost per experiment lower than that of skilled PhDs working manually in well-equipped labs. These costs limited what cell programmers believed possible.
But as Ginkgo scaled its platform, the scope of supported applications grew. With this growth, our costs continue to decline and our capability to perform synthetic biology grows. To give a sense of the scale economics inherent to our biofoundry, we see a 40-50% average year-over-year decrease in the cost per campaign. With such growth, our goal today is to continue to open the design of biology to more companies and pursue possibilities limited only by our imaginations.
Author
-
Paul Naphtali is a seasoned online marketing consultant. He brings to the table three years of online marketing and copywriting experience within the life sciences industry. His MSc and PhD experience also provides him with the acumen to understand complex literature and translate it to any audience. This way, he can fulfill his passion for sharing the beauty of biomedical research and inspiring action from his readers.
View all posts